So first job on the stock was to lay out the pattern
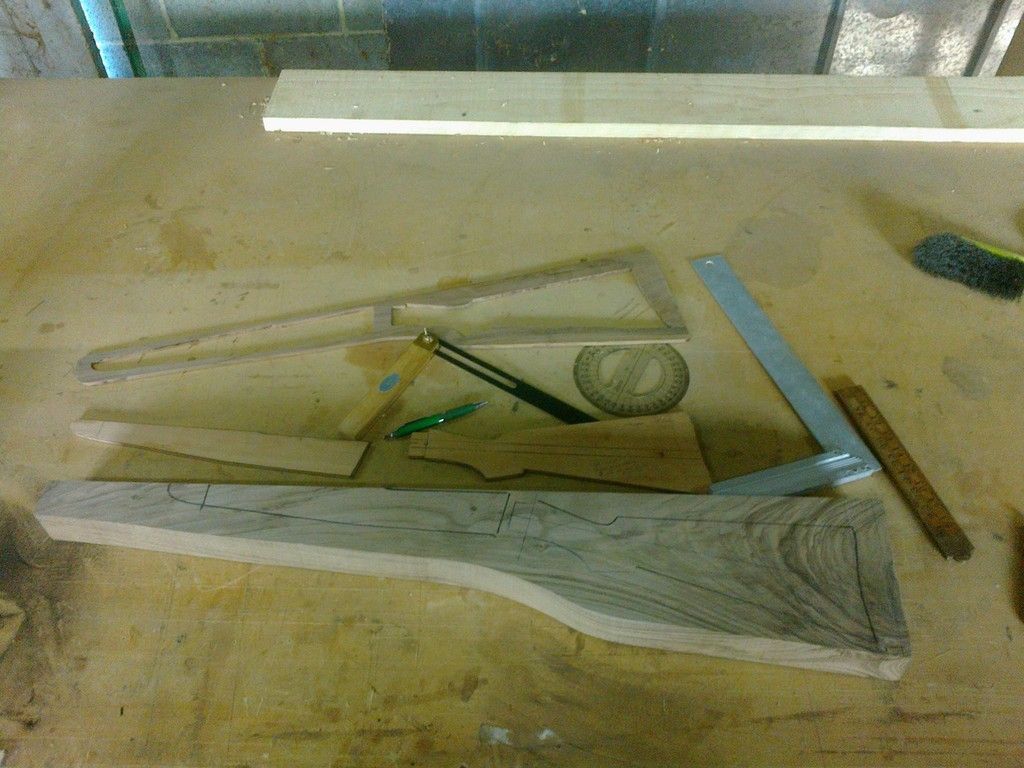
As an aside Bill required a 14 in L O P and if a line is drawn down the rear of the wrist socket and a measurement is made from the centre down the line for 2 inches, a 1/2 forward of this line is the face of the trigger so from there to a line through the centre of the stock bolt hole has 14 inches marked then the L O P should be as requested. At the same time when Bills preference for pitch was asked for, the same 2 degrees negative pitch that I did my own rifle was decided on. Our style of shooting and chest structure will dictate this factor in the design
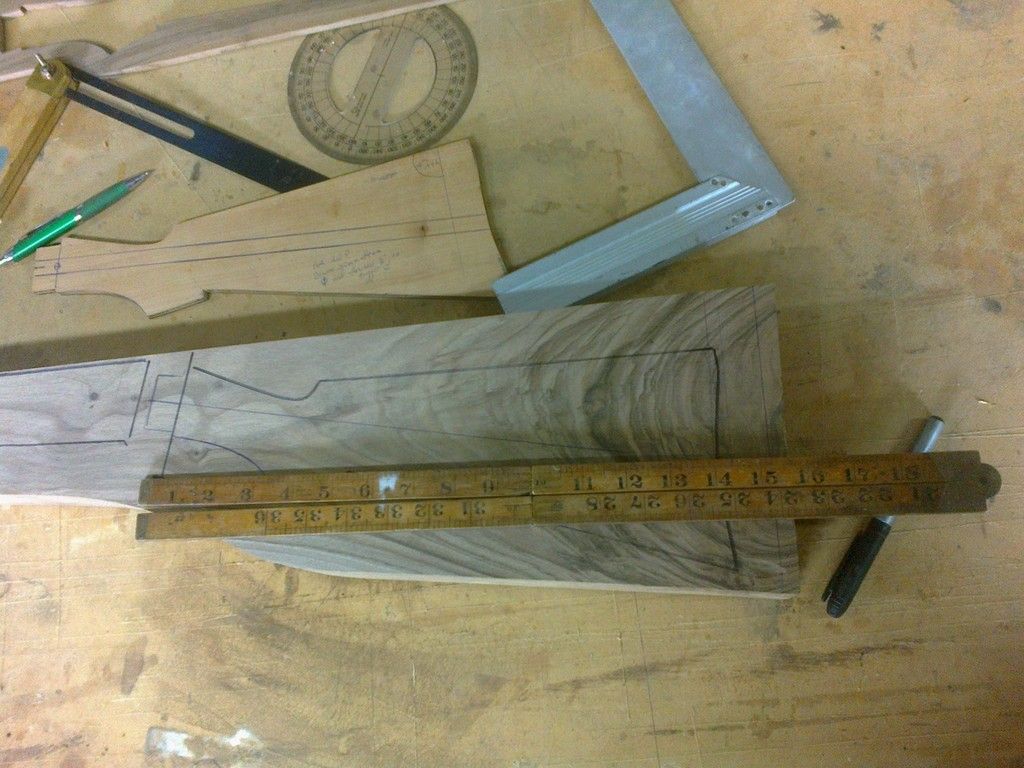
Something I have found to be advantagous is to (if necesary) plane the top edge of the blank so that the pattern can be laid out with the top edge of the blank coinciding with the top line of the forstock and then the angles can be more easily marked in and using the draw saw set to that angle the face of the draw against the socket can be made accurate. The same angle is used for the face of the socket nose
So with the pattern cut out and the grip cap, forend tip and the checkered buttplate all in order it was time to leave things for the day.
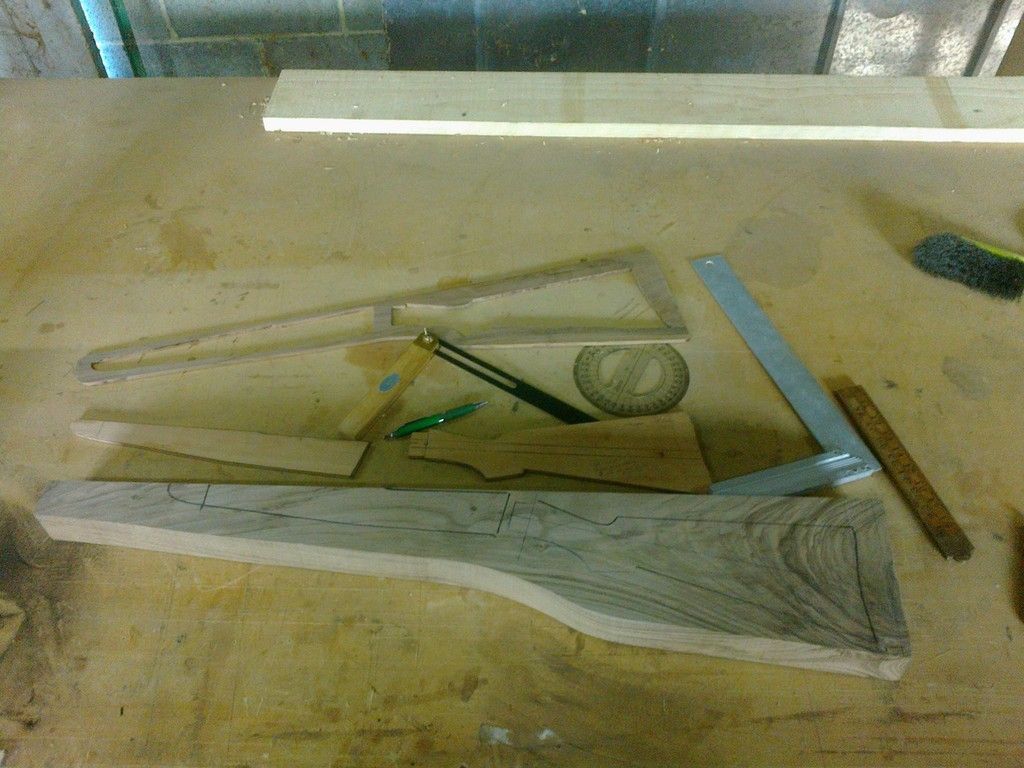
As an aside Bill required a 14 in L O P and if a line is drawn down the rear of the wrist socket and a measurement is made from the centre down the line for 2 inches, a 1/2 forward of this line is the face of the trigger so from there to a line through the centre of the stock bolt hole has 14 inches marked then the L O P should be as requested. At the same time when Bills preference for pitch was asked for, the same 2 degrees negative pitch that I did my own rifle was decided on. Our style of shooting and chest structure will dictate this factor in the design
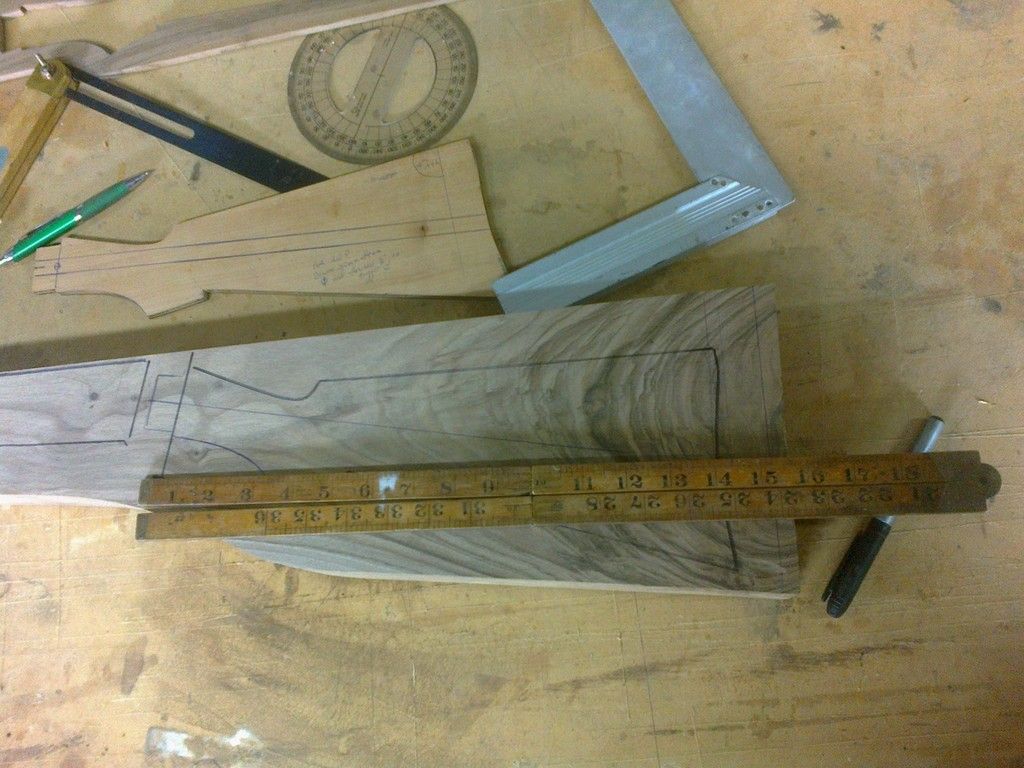
Something I have found to be advantagous is to (if necesary) plane the top edge of the blank so that the pattern can be laid out with the top edge of the blank coinciding with the top line of the forstock and then the angles can be more easily marked in and using the draw saw set to that angle the face of the draw against the socket can be made accurate. The same angle is used for the face of the socket nose
So with the pattern cut out and the grip cap, forend tip and the checkered buttplate all in order it was time to leave things for the day.
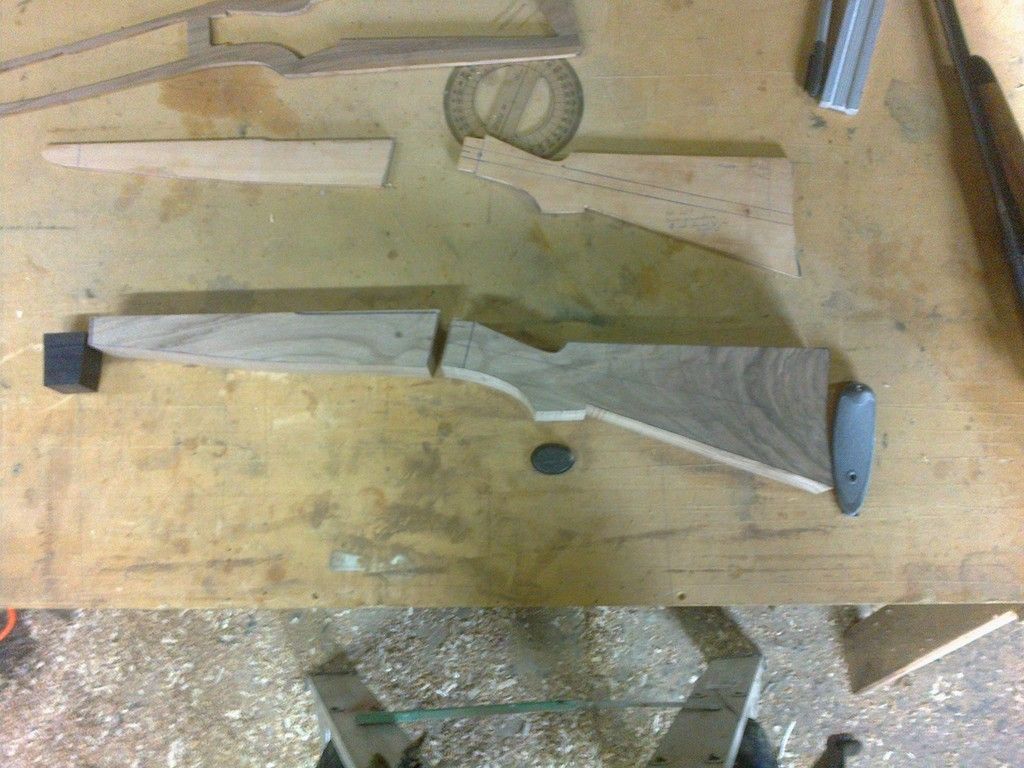
Comment